Identification and tracking system that withstands multiple cycles of heat
Control your extreme environment production
How to keep track of products or parts processed at temperatures of over 600°
Many manufacturing processes use extreme heat. Products or parts traveling along the conveyor from multiple production stations need to be identified and directed for further processing after they’ve passed, for example, through a furnace with temperatures of over 600°. Traditional forms of ID, such as barcodes or RFID (radio frequency ID), are destroyed at high temperatures.
Heat ID is a combination of AI-enabled vision and metal punch cards that are attached to products or parts as a means of identification. The solution accurately reads the cards’ data despite continuous motion and the inevitable damage from the heat. This allows to:
- Identify the part at any point of production
- Automatically control further processing
Key benefits
- Identification accuracy of over 99% in extreme processing conditions
- Accurate real-time location data for each of the hundreds of frames on the conveyor
- Significant reduction in production downtime through predictive maintenance
Typical applications
- Automotive industry – production of heat exchangers and bodyshell, painting lines, galvanizing plants and drying systems
- Paint and coating manufacturing
- Bakeries
Features
- Heat ID is available as a ready-made solution
- Minimal configuration to suit many production lines with conveyor transport systems
- Configuration includes camera, PC, identification software, communication protocol, tracking and routing software
- Minimal maintenance is required
- Reliably used in many projects – read a success story
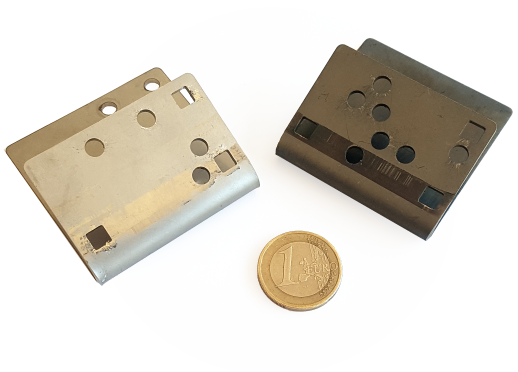
Punch cards created and configured to suit your production needs
For example, punch cards 50mm x 50mm in size (pictured) can encode over 16,000 numbers using error-proof ECC (error correction code).